The bellows is a kind of precise elastic vessel, and its manufacture requires accurate design calculations and strict quality management.
Generally speaking, the production of bellows is to fix the metal pipe and install a set of corrugated mold inside or outside the metal pipe. When the stress of the metal pipe exceeds the yield strength of the material, it will be formed according to the designed mold shape.
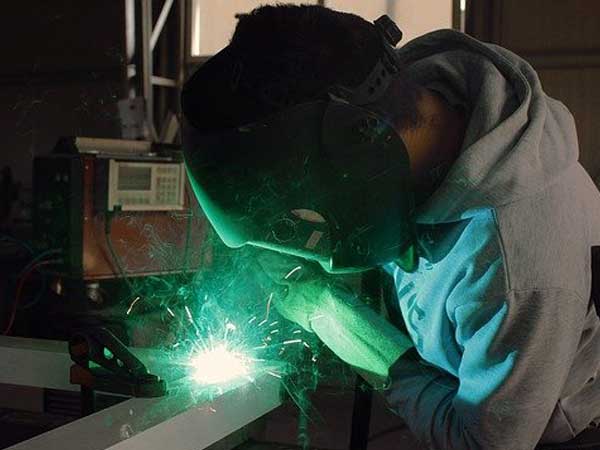
The specific production process is as follows:
Metal plate cutting
According to the size of the bellows, calculate the size of the metal plate, and then cut it. After the first cut, the size of the obtained metal plate is checked. After the inspection is qualified, continue processing, and conduct random inspections every fixed amount.
Metal plate rolling
According to the diameter of the bellows, choose a suitable reel to roll the metal plate into a pipe.
Surface Cleaning
Before welding, the surface of the welding area must be cleaned. You can scrub oil or dust with acetone to ensure welding.
Metal sheet longitudinal welding
Use a longitudinal welder to weld the rolled metal pipe.
Longitudinal welding seam detection
To prevent the metal pipe from cracking due to insufficient pressure-bearing capacity during the forming process, penetration testing is usually performed on the weld of the metal pipe.
Longitudinal welding seam surface treatment
To remove the surface discoloration and restore the corrosion resistance, it is necessary to passivate the weld.
Metal pipe rolling
Use the rolling machine again to roll the metal tube.
Formed bellows
- Hydroformed bellows
Multi corrugation forming in one step
Single corrugation consecutive forming - Mechanical expansion
Cuff cutting
According to the different connections of the bellows, there are many ways to cut the cuff.